Supply Chain
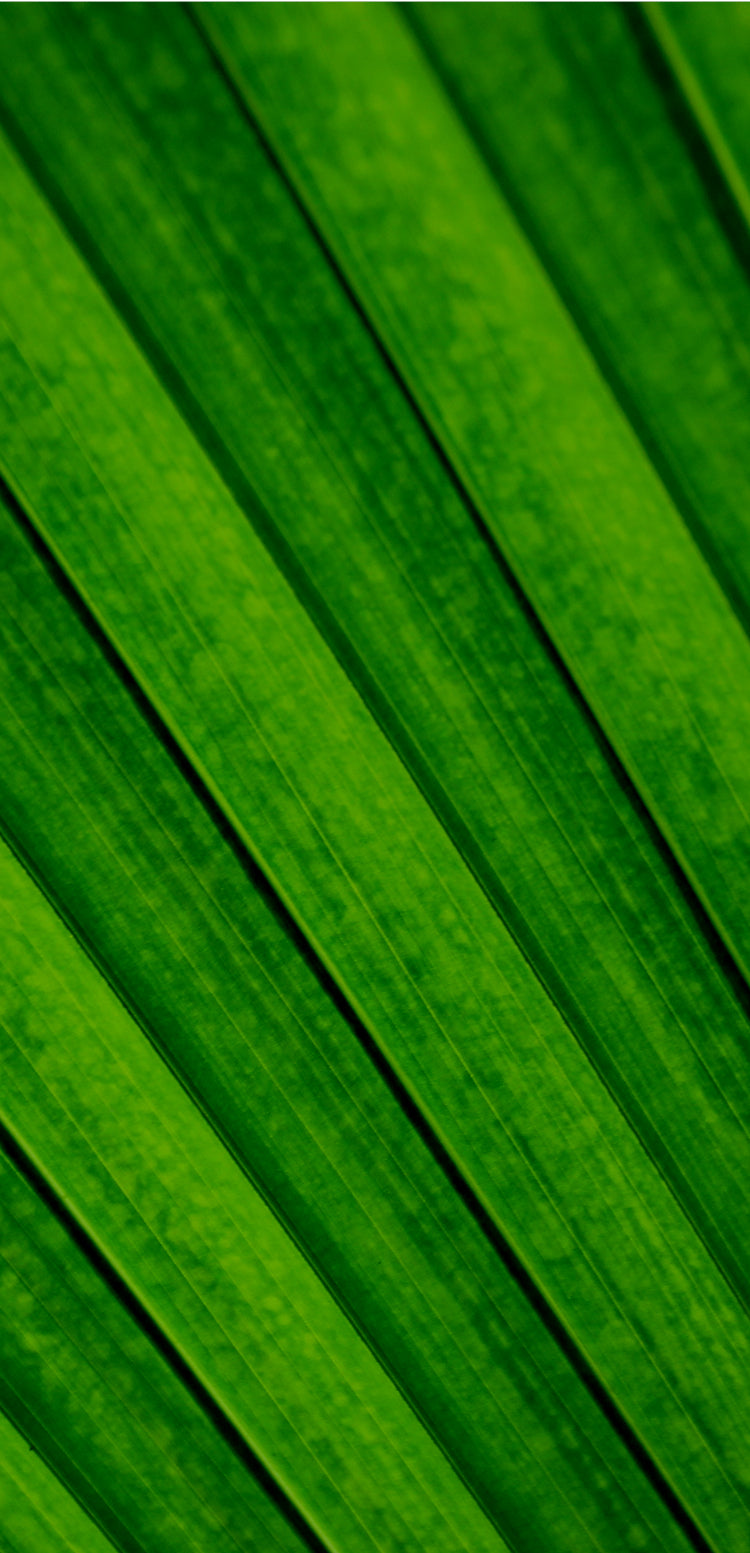
Bamboo: Nature’s Overachiever
Our story starts in the lush bamboo forests, where this incredible plant grows faster than your weekend disappears—up to 91cm a day! Unlike trees that take decades to mature, bamboo is ready for action in just 3-5 years.
Oh, and did we mention our bamboo is FSC-certified? That means it’s sustainably harvested, and our farmers are treated fairly.
Harvesting: No Bald Patches Here
When it’s time for a trim, we selectively harvest one pole at a time—no mass clear-cutting like with tree forests. That way, the bamboo forest keeps thriving while we take just what we need.
Translation? More happy pandas (and other critters), less destruction.
Chipping: Breaking It Down (Literally)
Once harvested, the bamboo gets chipped into small pieces before heading to the pulp mill. This step preps the bamboo for its glow-up—from humble stalks to soft, strong toilet roll.
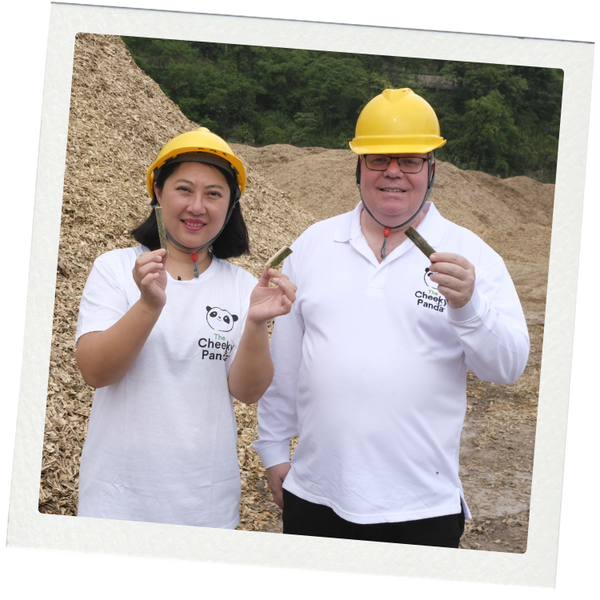
Pulping: The Secret to Softness & Strength
Here’s where the real magic happens. The bamboo chips are turned into a pulp, while keeping their long fibres intact (aka, the secret to our famously soft and strong TP).
We also keep things eco-friendly, using a process that minimises chemicals.
Rolling With It
Next, our soft bamboo pulp gets pressed and dried into 1-tonne parent reels (basically, toilet rolls made for giants) before being cut down to size.
Then, depending on how plush you like your loo roll, we convert those 1-ply sheets into 3-ply or 4-ply rolls for extra strength and absorbency.
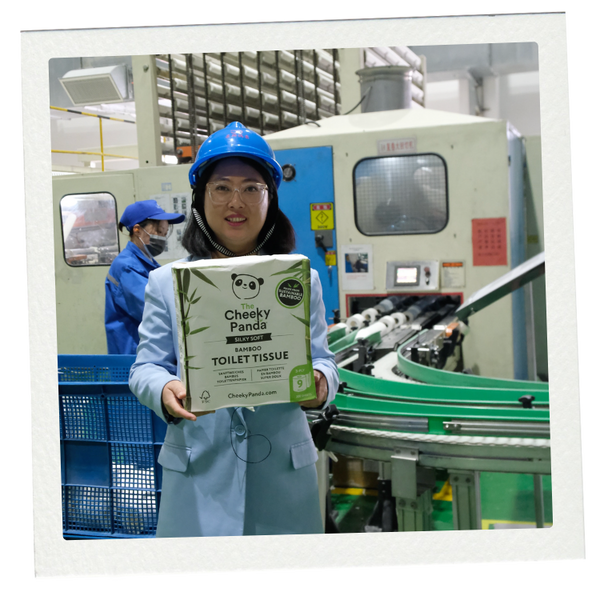
Only Perfect Rolls Make The Cut
Before our rolls make it to your bathroom, they go through strict quality checks to make sure they’re up to Cheeky Panda standards.
We test for:
✔ Pulp quality
✔ Paper strength & softness
✔ Flushability (because no one wants a clogged toilet)
✔ Hygiene & safety
Only the best rolls make the cut!
Shipping: Low Footprint, High Impact
We ship everything from China to the UK via sea freight—because it’s the lowest carbon option. Unlike some recycled toilet paper, which zigzags across the globe before even reaching UK converters, our supply chain is direct and efficient.
Translation? Less unnecessary transport, fewer emissions, lower footprint.

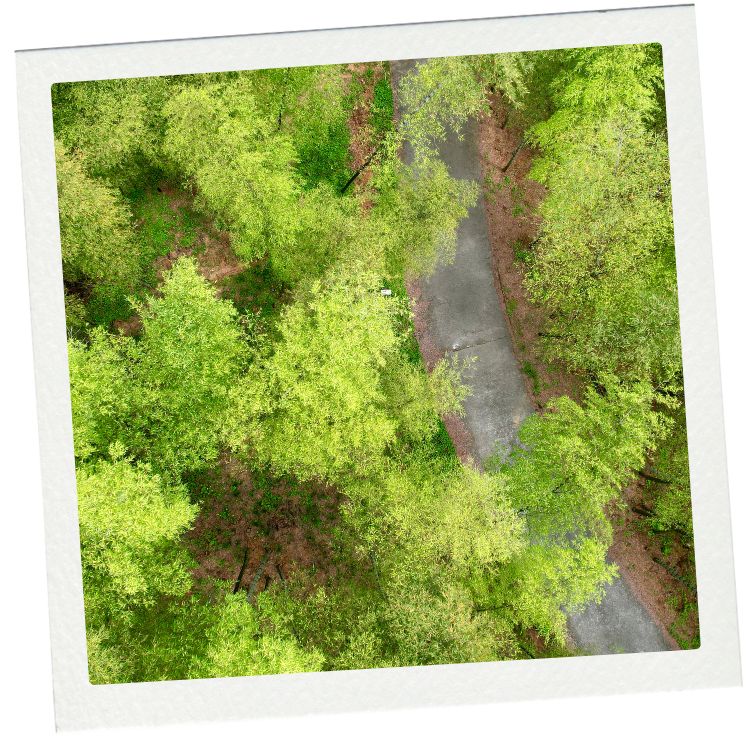
Fully FSC’d. No Forests Harmed.
We don’t just talk the talk—we walk the bamboo-lined walk:
Our bamboo is sourced from FSC-certified forests. This ensures no trees, people or animals are harmed in the growing and harvesting of our bamboo, in line with FSC’s 4 key principles: zero deforestation, fair wages and work environments, supporting the transition from preservation to conservation and local community rights. *chef’s kiss*
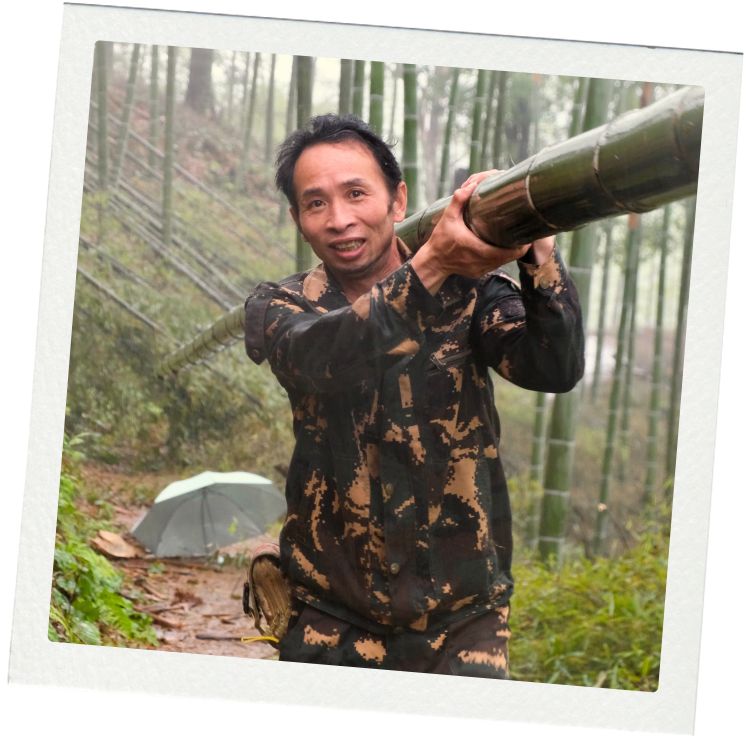
The Brilliant Humans Behind the Rolls
Behind our brilliant bamboo rolls, there's a whole bunch of brilliant humans. And we look after them.
That means fair pay, safe working conditions, and proper support across the board – from subsidised housing and meals for our production team, to enhanced parental leave and flexible hours for our UK crew. Because what’s the point of saving the planet if we’re not showing up for the people on it?
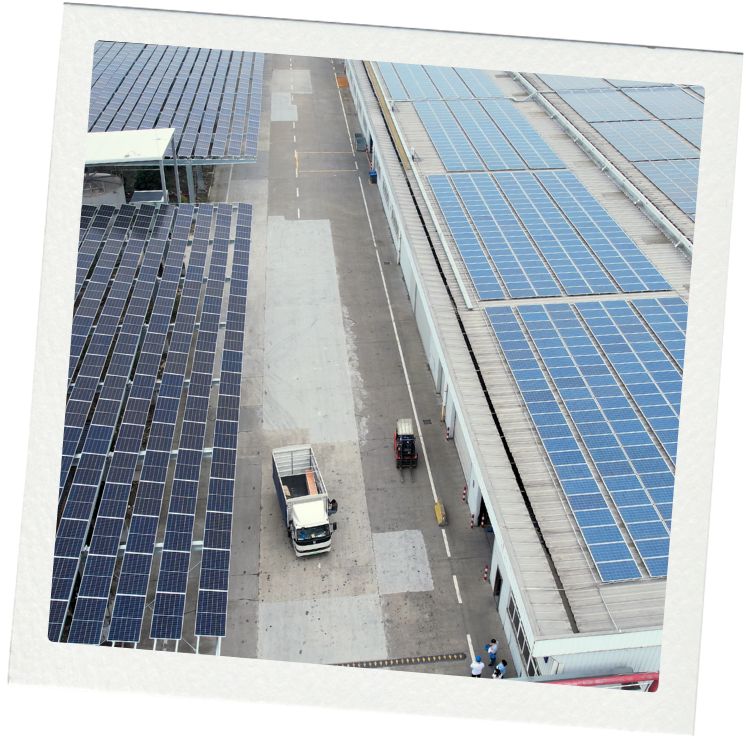
Sustainability Is a Journey (& We’re Not Done Yet)
We’re always looking for better ways to roll. Because let’s be honest – sustainability isn’t a finish line. It’s a work-in-progress (with some pretty exciting upgrades in the pipeline).
- Shift all of our production to renewable energy sources
- Pilot low-carbon logistics programme to further reduce transport emissions
- Continue researching ways to remove all plastics from our packaging and products
- Further reduce packaging material weight
